A Cost Saving, Quick Delivery Alternative
Arrow Gear is well known as a producer of high precision custom gears for a wide range of applications. However, we also offer a cost savings alternative to custom gears with our full line of spiral bevel stock gears.
Arrow provides 51 different sets of lapped spiral bevel gears in ratios of 1 to 1, 2 to 1, 3 to 1 and 4 to 3. In addition, Arrow stocks 8 different sets of ground tooth spiral bevel gears in ratios of 1 to 1 and 2 to 1.
All of Arrow’s stock gears are carburized and hardened on the teeth, and are produced in matched set.
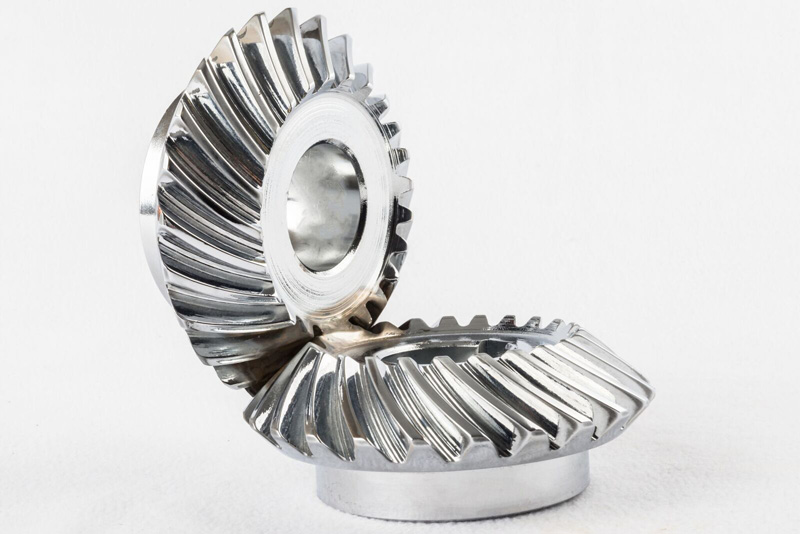
All of Arrow's Stock Gears are produced in matched sets.
What makes Arrow’s stock gear product line so unique, as compared to those of other stock gear suppliers, is the level of precision. Since our stock gears are produced in the same manufacturing environment as our aerospace industry products, customers can be assured Arrow’s stock gears are of the highest quality. Many Arrow customers use our stock gears in large scale production of their products. Still, many more use our stock gears for low production volumes or prototype work, integrating well designed, quality gear sets which translate to significant cost savings.
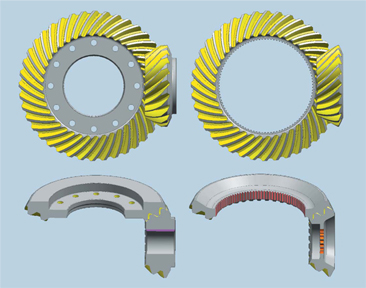
This illustration is an example of an option for modification of Arrow's Stock Gears. The gear on the left represents the stock design weighing 22 pounds. The gear on the right represents the modified gear weighing 12.5 pounds.
Modifications
To accommodate an even wider range of customer specifications, Arrow’s stock gears can be modified. Available modifications can include changes to bore size, keyways, and hub length. These features can be machined at a very reasonable price as compared to placing an order for custom gears.
Please review the other topics in the stock gear section of our Website for more information on our stock gear product line.